Before I show a fix , I should mention that the clubs in our area have been running various F1 classes for quite a few years, most with higher power motors than we will be using, and failures/breaks in this area, are very very rare, so, while bracing is a good failsafe, do not feel that it is necessary for strength. Bracing the rear end is much more critical from a performance perspective, but with the motors we are using for this proxy, do not feel that it is required in order to be competitive.
A little background...It is virtually impossible to make the triangle formed by the motor shaft (pinion) and the two axle bearings stiff enough (this applies for any motor configuration...inline, side/angle winder). Flex in this area is the cause of many things that are not great in a slotcar.....inconsistent/bad gear mesh, bushings binding on the axle, and the most visible.....chatter/axle hop !!. To get a visual at home, grab a complete rolling chassis, hold the motor and rear axle in opposite hands and give it a gentle twist/torque.....if you see flex/distortion in the uprights, and movement between the pinion/spur/crown, some beefing up will certainly not hurt.
Now before you think that all your cars must be rebuilt, some flex in this area is inherent, particularly in plastic chassis' cars, and unless you are noticing chatter/hop or are having excessive gear issues, you are likely just fine. Excessive flex in this area is noticed more in cars with stronger motors, grippier tires, and on high grip/ wide radius cornered tracks.
The rear ends on most of the Scaley F1 cars are not hideous, and the motors we are running are not strong, so, again, do not feel that bracing in this area in necessary to be competitive.
Now, for those that don't believe me ;) , I will show an easy way to brace the rear uprights/motor mount face.
You can use strips of styrene, brass/aluminum strip, or piano wire glued to the inside of the chassis, tying in the motor mount face and the rear uprights. Each Scaley car is a little different requiring a different thickness/shape but the goal is the same.......tie the motor mount face to the axle uprights.
For glue, I prefer Locktite 380, but any rubberised CA (IC2000 etc.) is perfectly fine.
*****It is not a bad idea to secure your bracing piece (s) before installing the rear bushings......a brace that does not fit perfectly, and distorts the rear uprights even a snick may be enough to "unalign" your previously aligned bushings.
Below are pics of two older Scaley cars done with braces many moons ago...........
The first is an older McLaren (2005)......it allowed me to bend a "U" shape of .032 brass strip and glue it along the motor mount face, and under the bushings.
****Depending on the height of the strip you use, you may need to grind a relief in it in order to clear the motor bushing motor shaft.....I had to do this on this car.
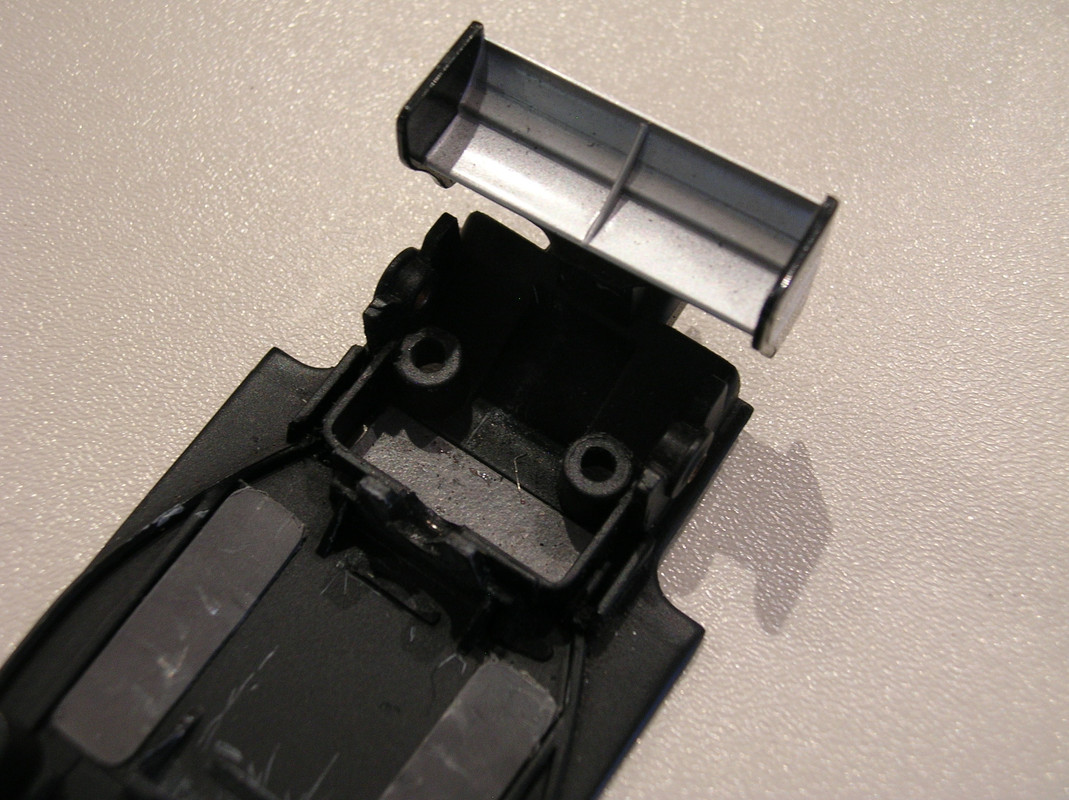
The next car is one of Kimi's 2007 Ferraris......a different design chassis plate made me use some thinner brass.
This pic. is not great, but the brass is glued to the motor mount face, and the "legs" run under the bushings...all the way back.
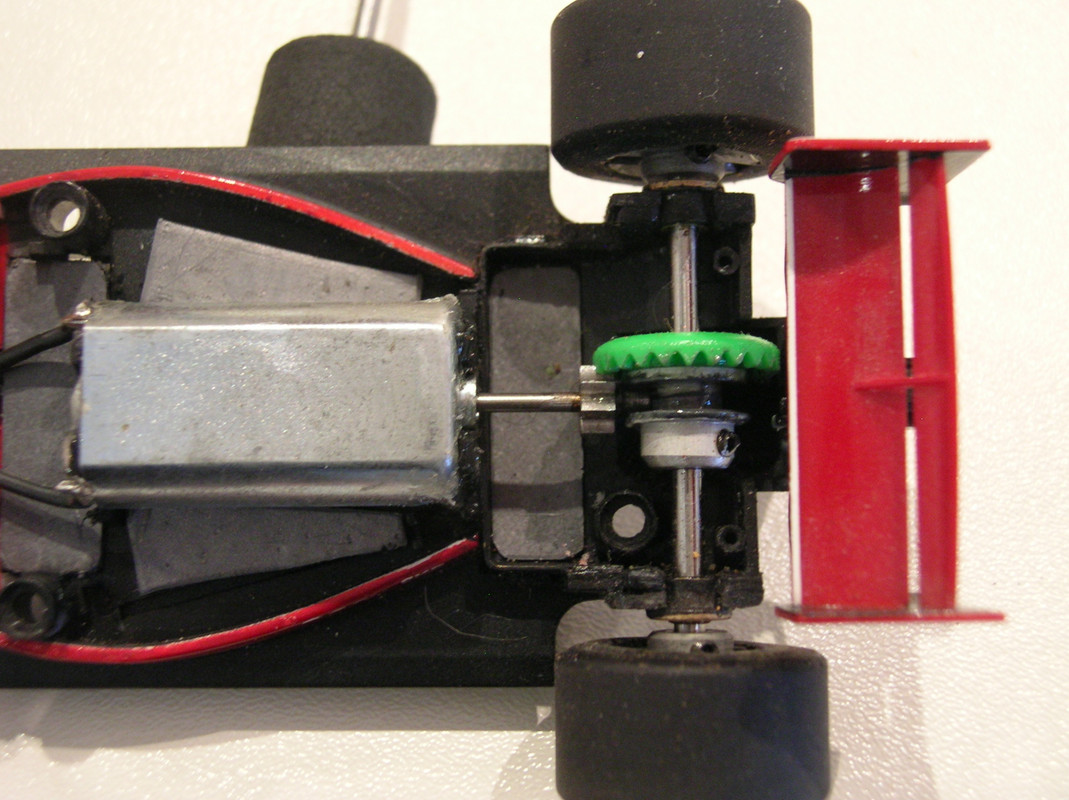
I have used piano wire bent into a "U" (.047/.055 is more than enough), sheet aluminum, and styrene (strip and square).......all work equally well, but, unfortunately don't have any handy example pics.
If anything is unclear,or more details needed...shout!!
hope this helps
Cheers
Chris Walker