Yea - somebody around here must know something about 3D printing.....
This one has got to be in my wheelhouse! :teasing-blah:
I'll be the first person to admit I don't know it all.... But I'll take a stab at a little explanation... :liar:
I think it's important to understand what happens first of all.....
Shapeways creates our chassis with what's called an SLS printer (Selective Laser Sintering). If you look at a chassis from the side - then imagine that chassis sliced into pieces of paper - that's how the machine builds. The machine shoots a laser into a bed of fine powdered nylon for one sheet - then the part drops down - is covered with powder and shoots the next sheet. until it builds up the shape in layers over a couple hours.
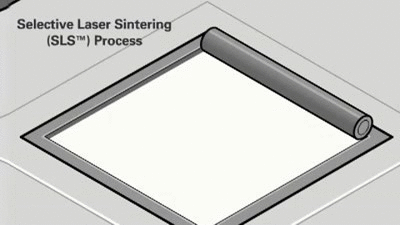
To break it down a little more - when the laser hits the powder - it melts. It makes a small ball of goo - and then the laser moves over and melts another ball of goo - and the two puddles of goo bond. When a chassis is done - that's why it has a grainy feel to it - its a bunch of nylon goo pellets that all melted together.
This is a close up of an sls part - not soccer balls (though they do look very similar for some reason - trust me - not soccer balls)

The curl will occur during cooling - when the stresses start to even out.... Since its Christmas and I know we all wrap our own gifts neatly- Imagine you have ribbon and a pair of scissors. If the scissors are cool air and the ribbon is the part - and you run the scissors over the ribbon - it curls. because the ribbon doesn't all cool at once - it moves from one area to another.... Inducing different stress and viola - warped part. Now - size and shape influence what happens - and you can't control all the conditions (humidity plays a huge part with nylon - but I digress).
So - to flatten an SLS part - is not easy. It has incredible memory and to dump the stress forces out of it - you have to take it close to melting the balls of goo. The nylon melts around 350F. What that softening curve looks like I'm not sure - it may be solid at 300 and melt at 350..... It may be solid at 349 and melt at 350....I probably have enough spare parts around to test certain conditions - so maybe over Christmas I'll devise a way to surmise a guestimate on the temp/time. I've had it in boiling water for 5 minutes and nothing moved.... In the end (as I've found out....) you have to design the material thicker or design in thicker supporting structure..... Also when you start to move the soccer balls around - you may actually pull it apart and degrade the strength. It may be flat - but may fail someday. To SLS a chassis based on traditional injection molding sizes won't work - it's too thin and will tend to warp in the <1mm areas - I think more than a few people making 3D chassis have found this out.
Sloting Plus and 1-2 others make 3D printed chassis as well - this is done through filament printing. I always explain this as a hot glue gun going crazy.... There's 100 yards of solid material and they run it through a super hot nozzle that squirts out with a little more control than a hot glue gun. It's builds up the same way with layering except its a liquid (sort of).. Getting the warp out of a filament print is somewhat tricky as there are so many materials available (different melt points) but since the chassis is a solid - the stress leaves fairly easy - but you have to know the material that was used....... Filament drawback is usually brittleness and I don't think repeated heated cooling will be good... I've avoided filaments for the most part - but I'm switching over to one in 2017 for certain chassis as the material is getting much better. Our line of guide adapters are made from a filament printer - but the material has chopped carbon fiber to help with strength etc.
I think the best answer is not easily - but I'll test it after Christmas with some old chassis I have. It will be like an episode of Myth Busters with explosions and test dummies I'm sure....