By Peter:
with the big scratchbuild proxy comming nearer and nearer, i wanted to start with an entry. Decision was a homemade body, MCE Centenaire, vac-formed from a Bburago diecast with a styrene chassis.
for a start, i took the measurements on the body - width, wheelbase
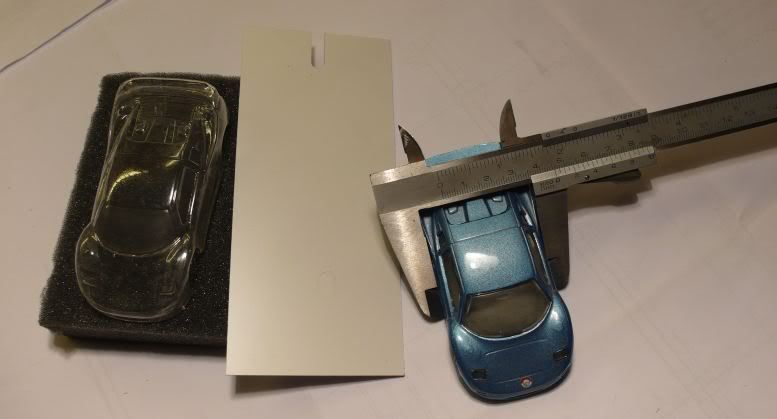
what will be the distance from the guide flag hole to the front axle?
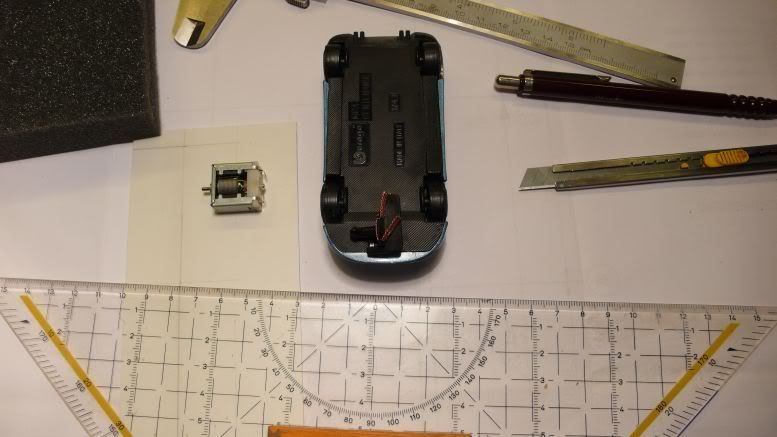
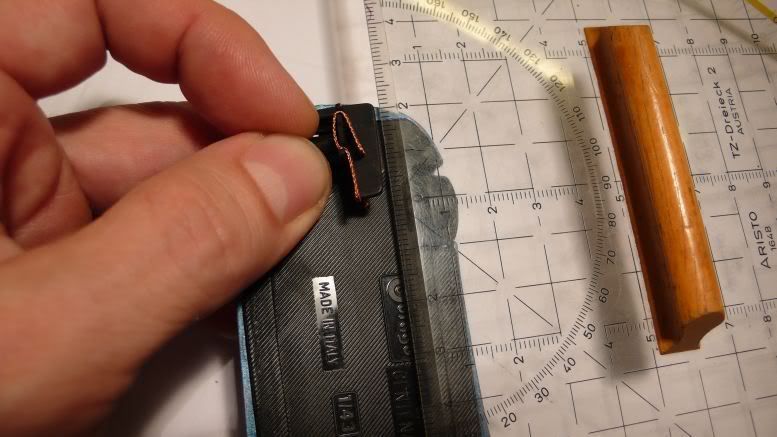
next step - aplly all data to the PS sheet, also the size of the wheels, to cut openings big enough for the wheels, plus a little space. i want the base plate of the chassis as wide as the body is.
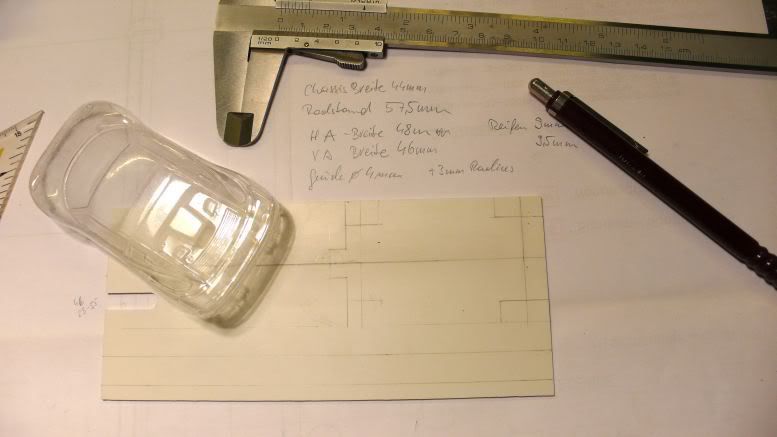
cutting the PS sheet with a cutter is quite easy. the thickness of my PS is 1.5mm.
all parts are on the table.
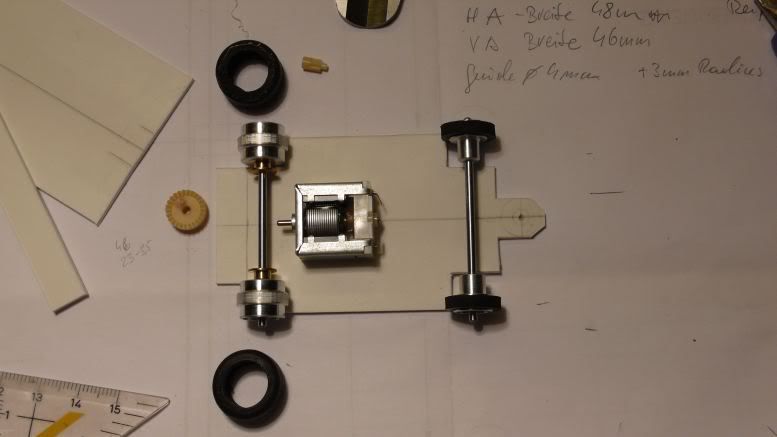
measuring the distance from the rear axle to the rear cross brace
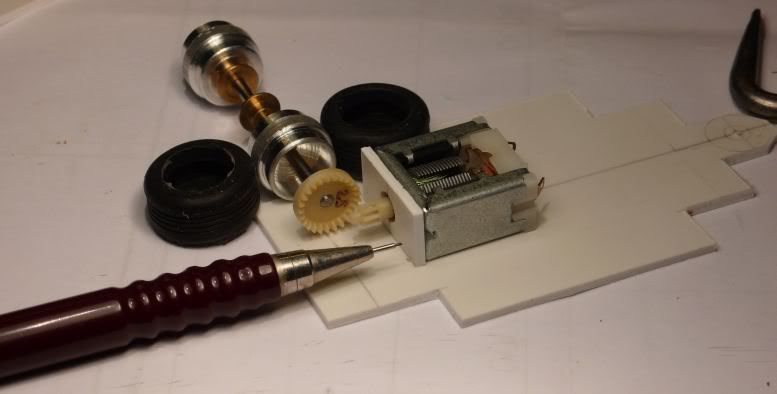
marking the wheel base and the length on the longitudinal braces, right away from the base plate.
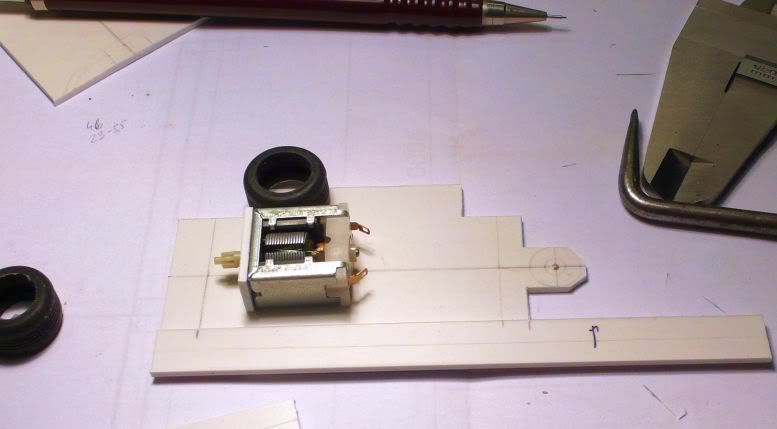
the height of the rear axle depends on the height of the motor. measuring the height of the motor, half of it is the height of the center line of the rear axle.
i drill one longitudinal brace first, than lay it over the 2nd and drill them together. first the front axle hole, put an axle in, then the rear axle hole. in this way both will have the same wheel base. note the front axle hole is lower, as my front wheels have 13mm diameter and the rears have 17mm. so the front axle hole has to be lower by 2mm.
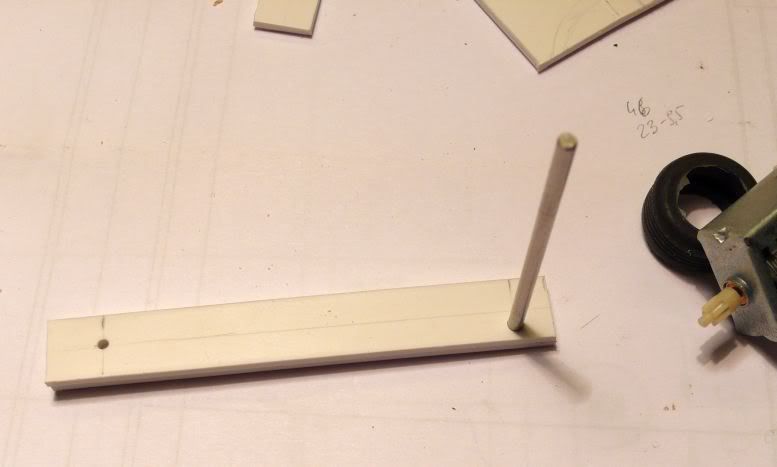
put the ranch-design bearings into the PS and pre-assembled:
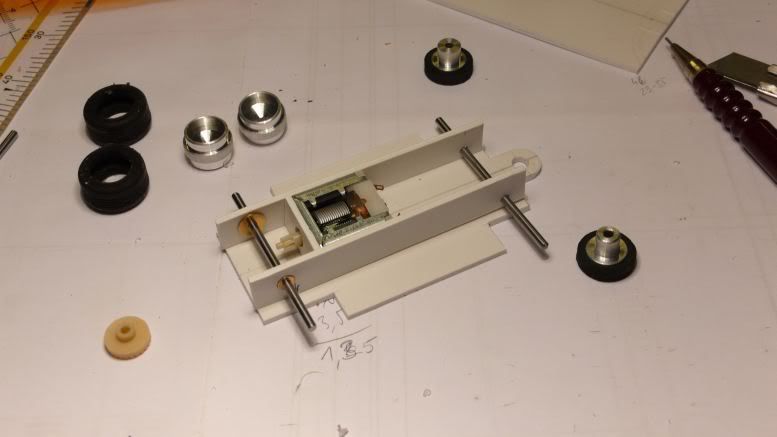
next step: glueing the longitudinal and cross braces to the base plate.
more pics to come.
puddle dude
Part 2
here is the next step: i glued the base plate with scotch tape to my setup block, to see if the rear axle is perpendicular to middle line - needed for good traction:
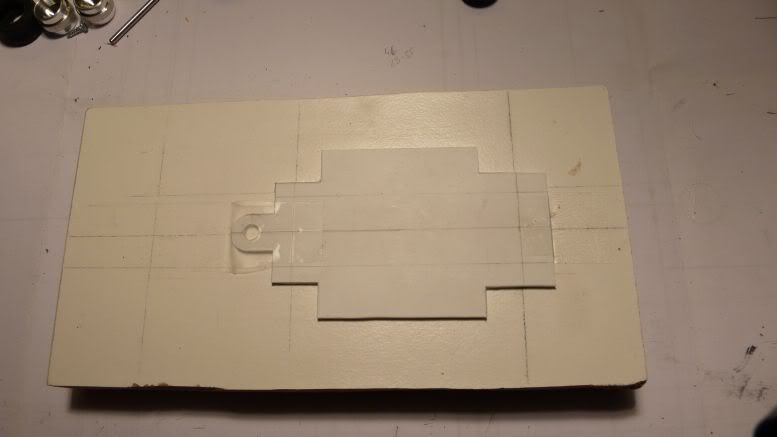
ranchdesign bearings glued into the side braces before glueing the side braces to the base plate, then revell glue to the side and ACTION.
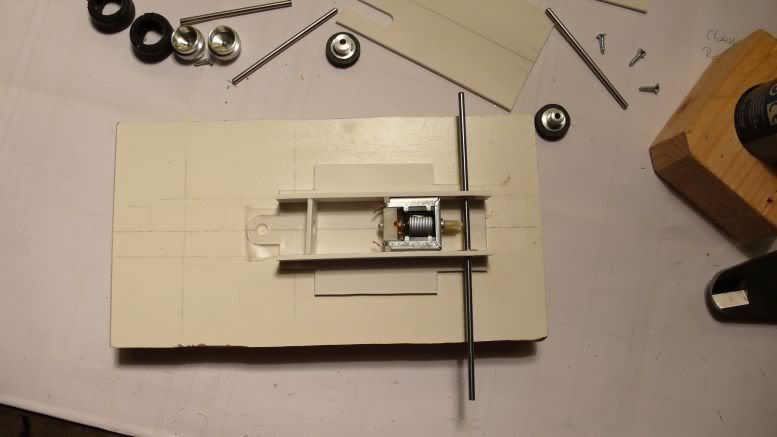
now i´ll let the glue settle until tomorrow evening (learned that part!) to allow real hardening
Mas, in the end i let my eyes do the last check, too. but during the first phases, i measure a lot. saves some time afterwards (maybe). And the rear wheels are stock artin replacement wheels from ranch-design. K&D racing tires are my choice for the tires.
Chuck, yes i like the body. the wheel base is right on the long artin plus it is WIDE. enough place to work inside. plus it looks cool (for me).
Marioyee, you´re welcome. glad to help.
Tom, i cut the styrene with a cutter or even with an old jigsaw (you know like the ones you get a kid to cut thin plywood, that´s the one i still use). let´s see what you use!
Part 3
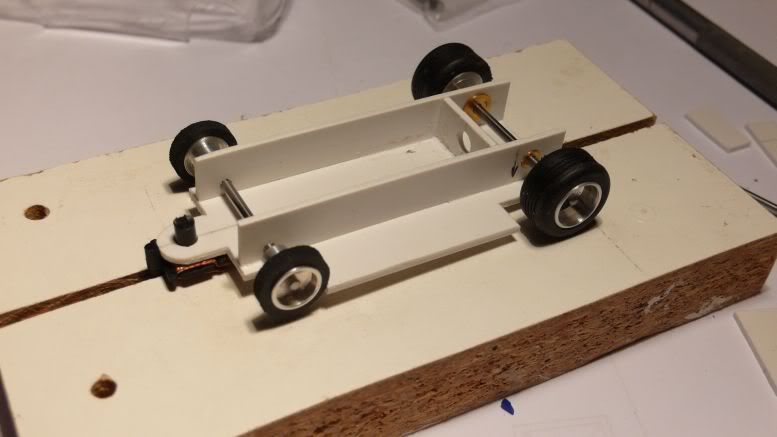
the guide (from RD) had the top cut off to fit under the hood. It has to go higher, so i´ll cut the inner front piece out and glue another piece over the existing. in this way, the guide will sit high enough in the chassis to allow the front wheels to touch the track slightly. Also found a little warp in the ready glued chassis. I´ll fix this as i put the chassis in hot water and than twist it slightly in the opposite way of the warp and let it cool down (this process can be fastened by putting the chassis under cold water ).
I´ll be satisfied when all 4 wheels touch the track at once without wobbling when pushing down at one corner.
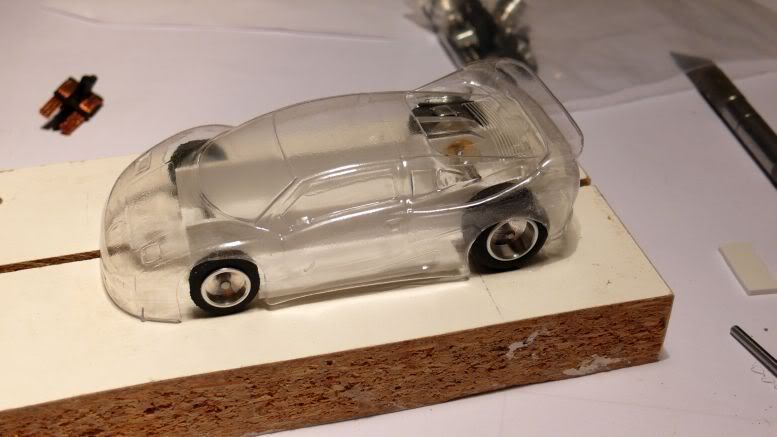
now also look to get the body easy over the chassis, the side will be shaped along the body lines.
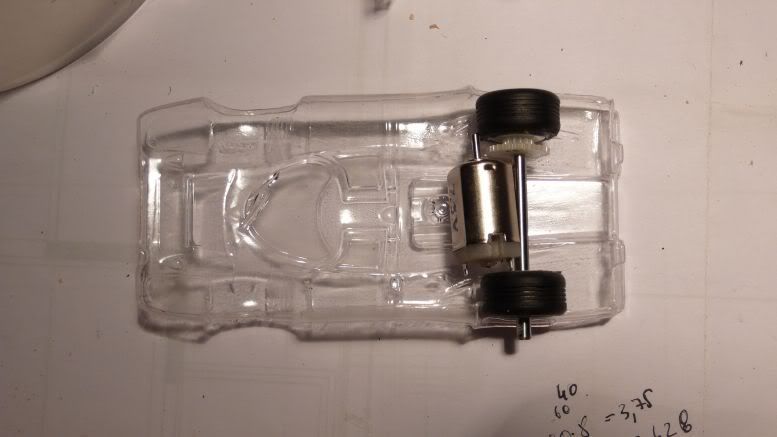
i think for this motor/gear combination i´ll also have to build a chassis by myself. seems to fit nicely inside the body i´ve choosen. a bonus banana for the first who guesses the body right
puddle dude
Part 4
marking the extension parts for the guide as it needs to go higher in the chassis
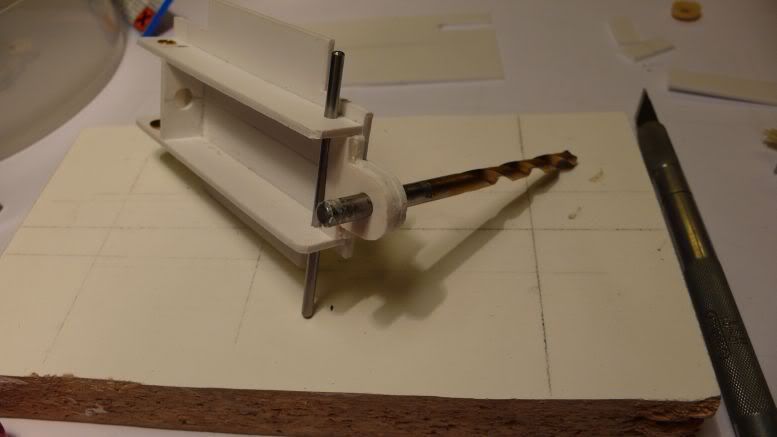
parts cutted and glued to the chassis, the will be filed down after the glue has hardened.
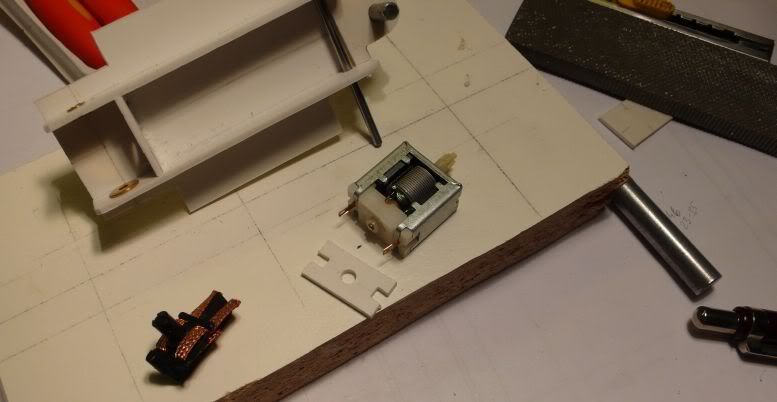
cutting the 2nd motor mount, holes for the wires filed out
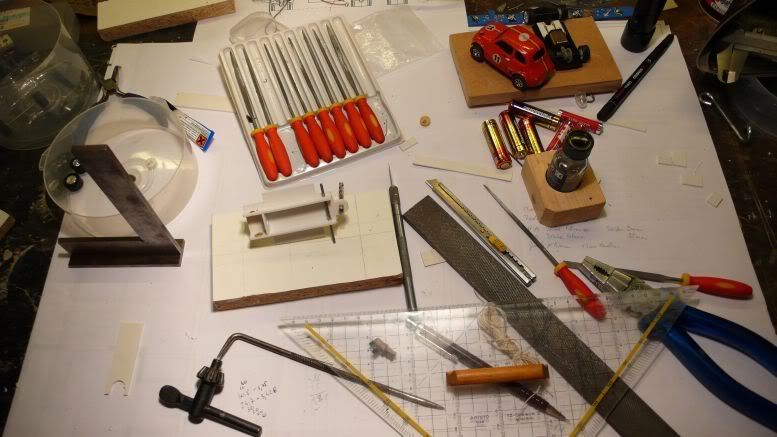
work bench is in the normal mess again
Part 4
Ed, thanks, i´m using modell glue from Revell for glueing the styrene. Applied with the brush that comes with the glue (inside the top cover of the bottle)
and Mas is the winner of the banana - here it is image
Steve, are these enough hammers?
normally i start using the hammers after the build is ready, for setup issues
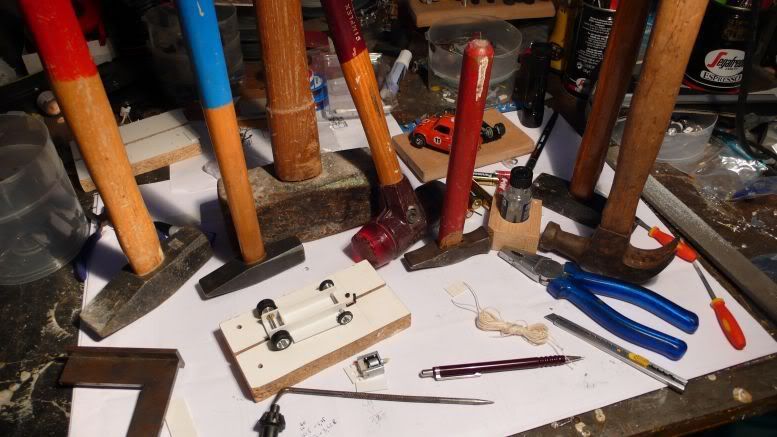
setting up the braid, the top right braid is stock, the other are in form already. to get the top side of the braid nicely flat to enable easy rotation of the guide:
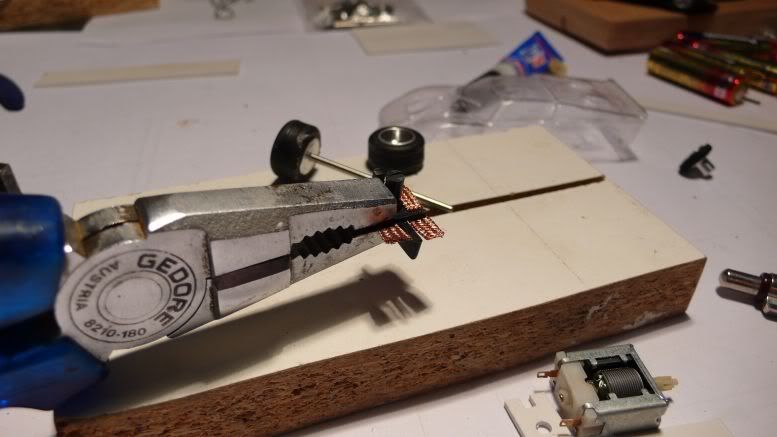
shaping the underside of the chassis to allow the guide to get a little deeper into the chassis. the part of the guide holder outside the longitudinal braces was filed down, for the circular part the dremel was used.
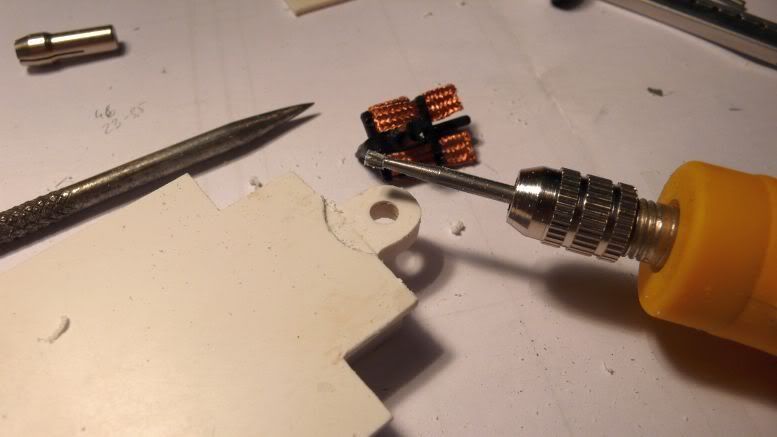
controll of the works: the front wheels should go up a little in the chassis, this clarifys Steve´s question if i can use all the measurement gears - NO even that or i can´t calculate
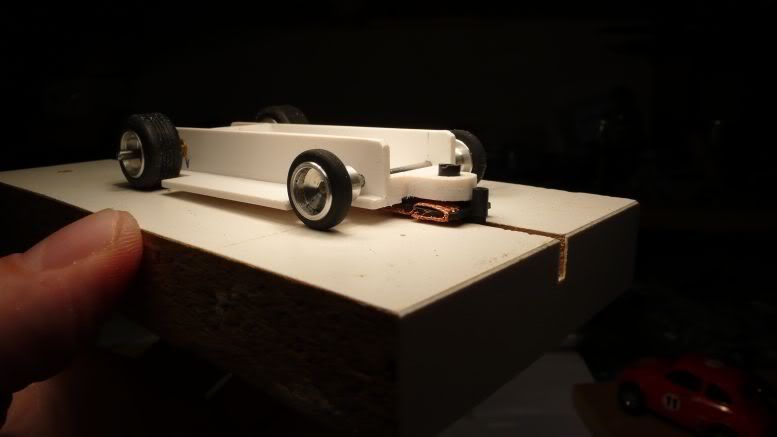
drilling a hole inside the guide to be able to fasten the guide in the chassis:
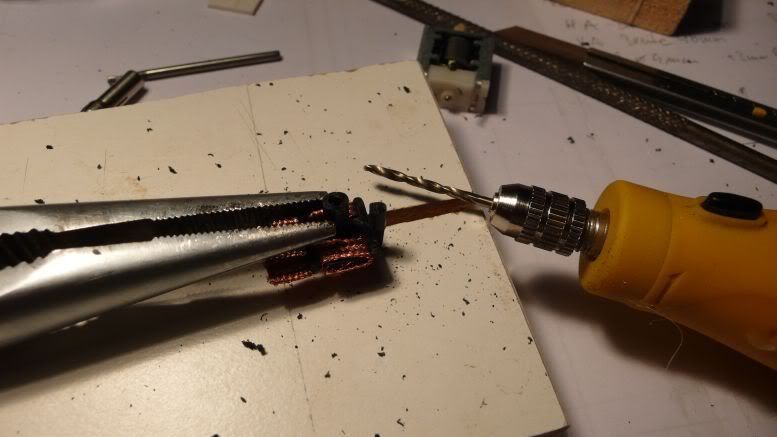
using a thread cutter M2, cut thread by hand worked great. now there is something for the screw to grub into
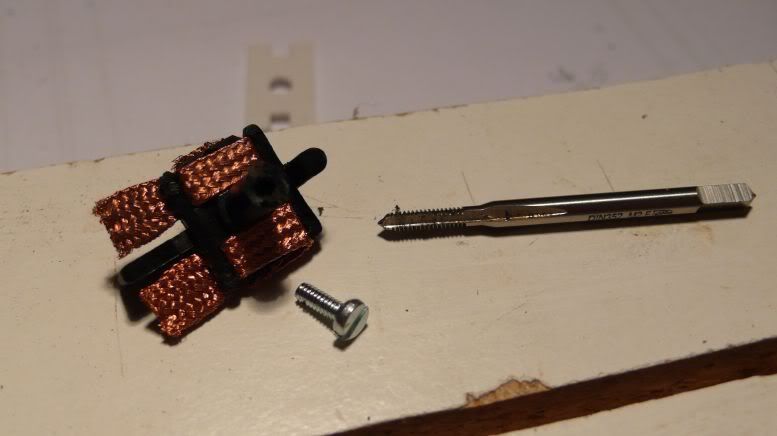
Part 5
the rear wheel wells will have to be widen a little, using the sanding drum in the dremel will do this job:
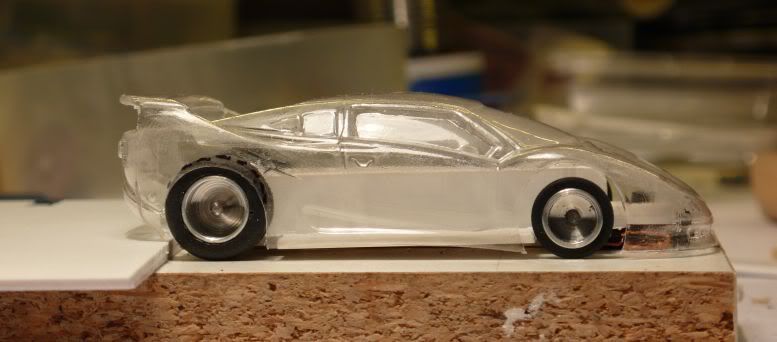
soldering the high flexible guide wire to the RD guide, i use some extra flux (as can be seen in the lower left corner of the pic) to get an easy soldering point. soldering the wire to the outside of the braid will allow an easy rotation of the guide.
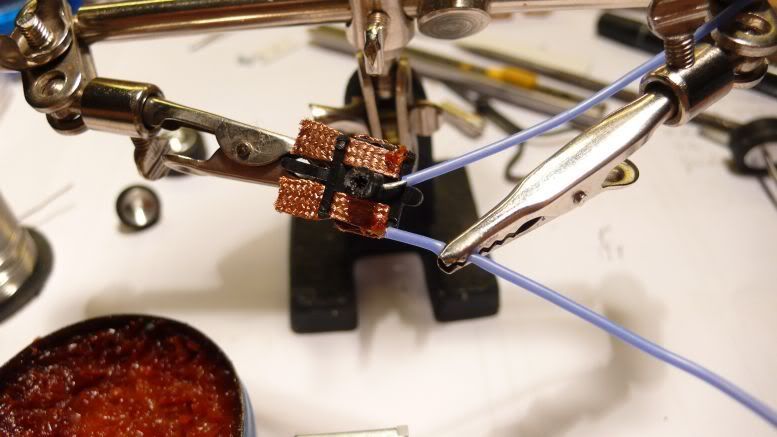
soldered the wire to the motor as well and glued the motor cross brace into the chassis. the 2nd brace holds the motor, so no glue on the motor and only on the side of the cross brace, to allow an easier removement if that should be necessary.
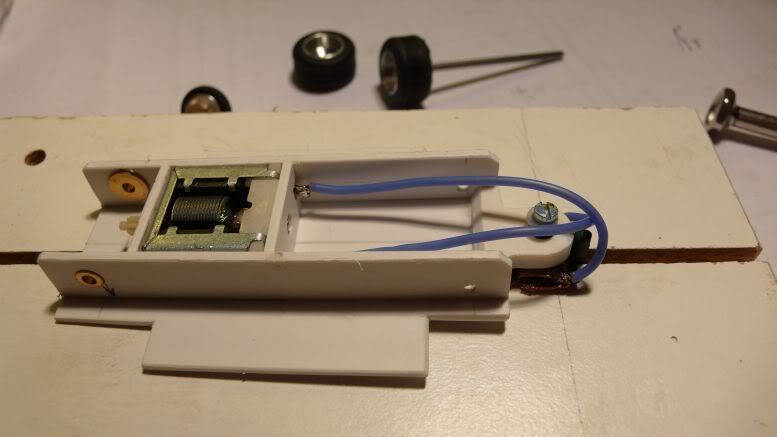
checking the axle lenght, i mount one wheel, mark the other side and then cut the axle with the hand steel saw. rounding of the edges of the axle with a fine file.
Notice also the styrene pipe parts - spacer to get the right width of the front axle.
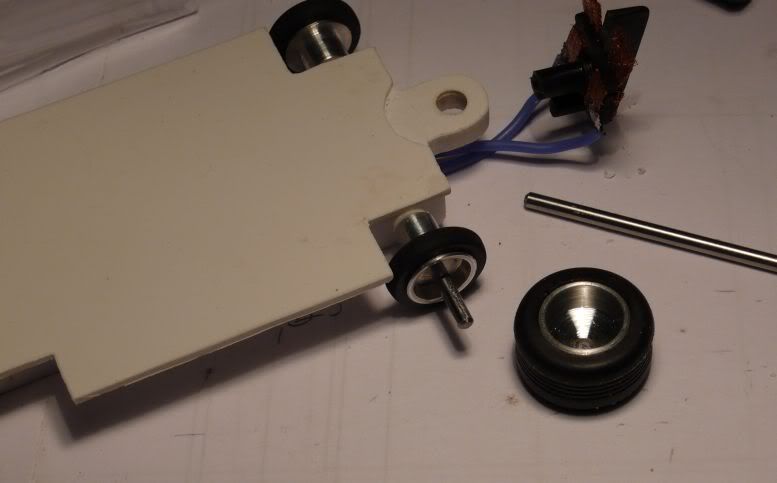
filing down the last amount of axle
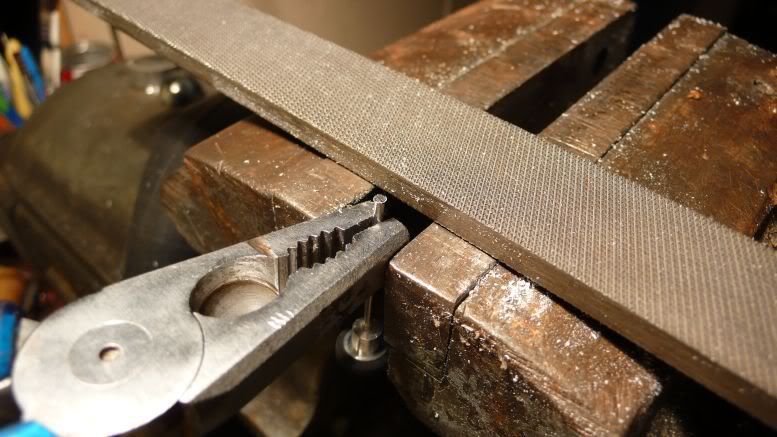
the crown spacer pipe is glued to the chassis and trimmed with a fine file to the right length.
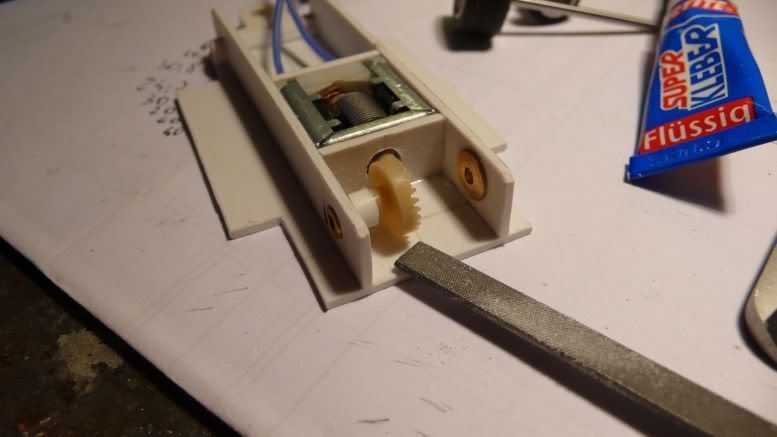
i glued the wires to the sides of the chassis so they stay in place and still have enough movement, just near the front axle.
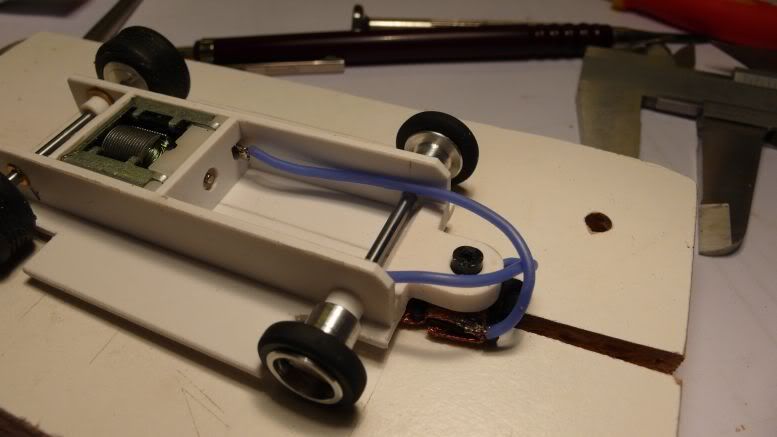
Part 6
next step on the personal todo list: glueing the tires to the rims. always a hairy thing to do ruined some tires in this way, but in 19 out of the 20 cases it works great.
apply CA inside the tire and put it over the rim.
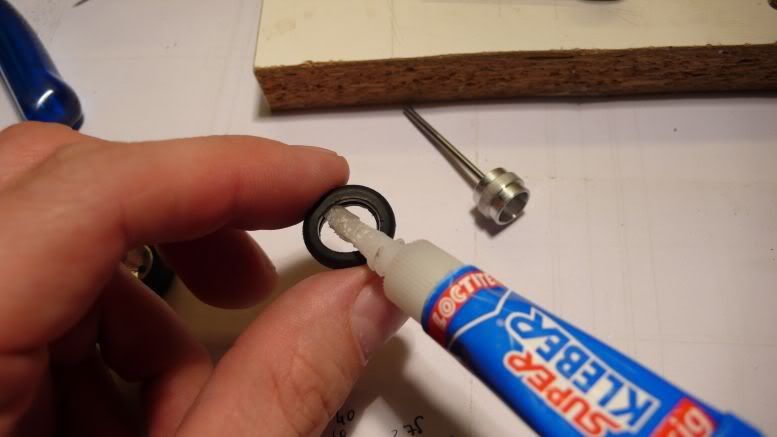
putting the axle into the chassis, push the crown to the crown post, not the other way
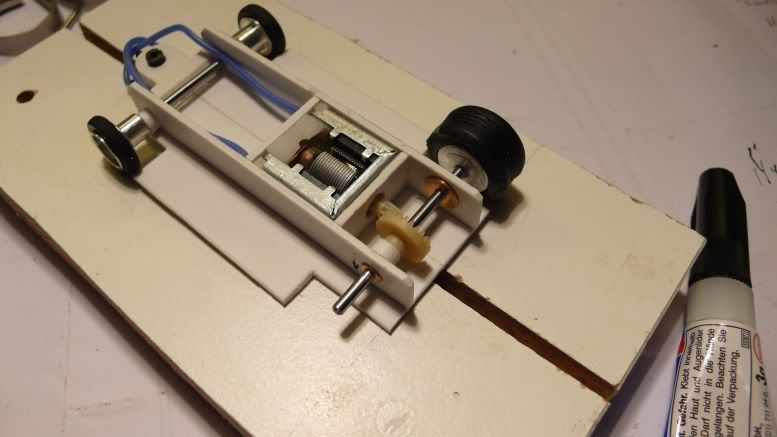
2nd wheel is glued to the axle, putting small drops of CA under the tire under the parts where the glue did not go in the first step. sometimes i think if it would be better the glue the whole tire in this way to the rim?
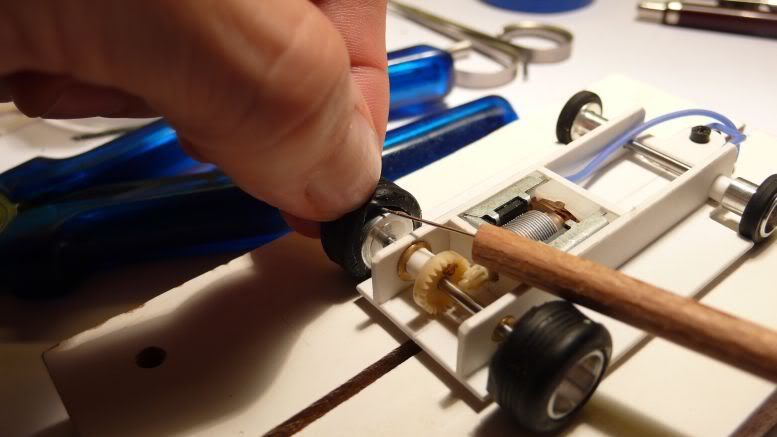
before i start with tire sanding
, i aplly pumice powder (with a little water) to the pinion/crown to help breaking it in. could also be done with toothpaste. i use the pumice powder also with a toothbrush to clean/sand resin bodies.
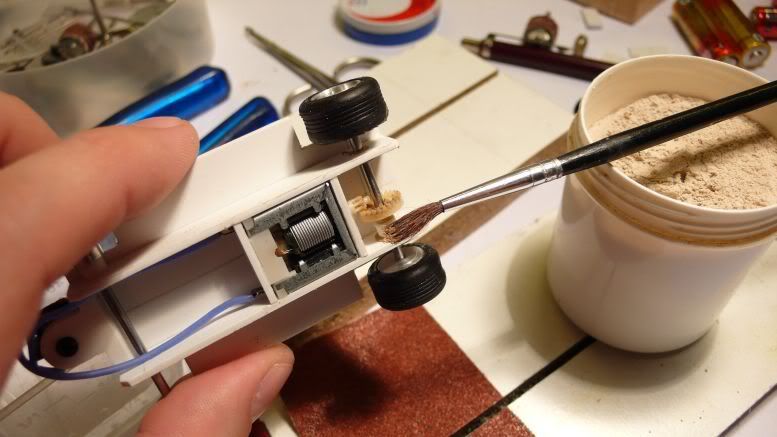
slightly oil the axle
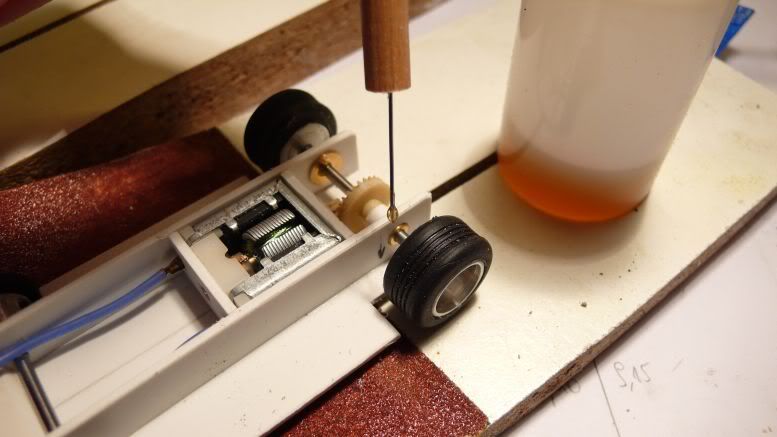
start sanding - always watch the motor temperature and the tire temperature while tire sanding
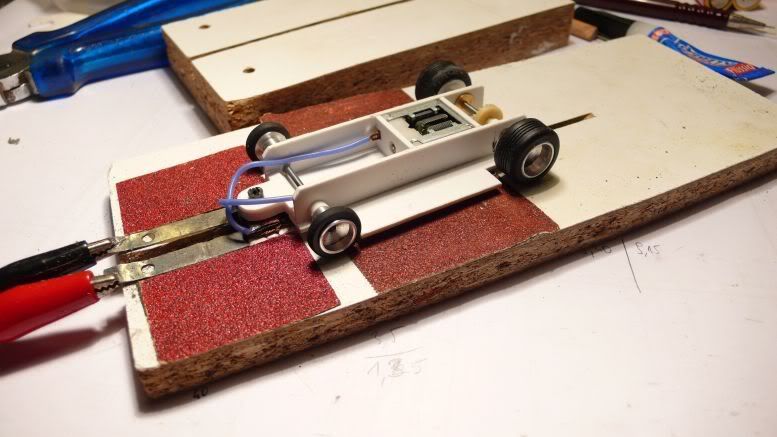
after the first sanding, the tire are getting quite good contact now ...
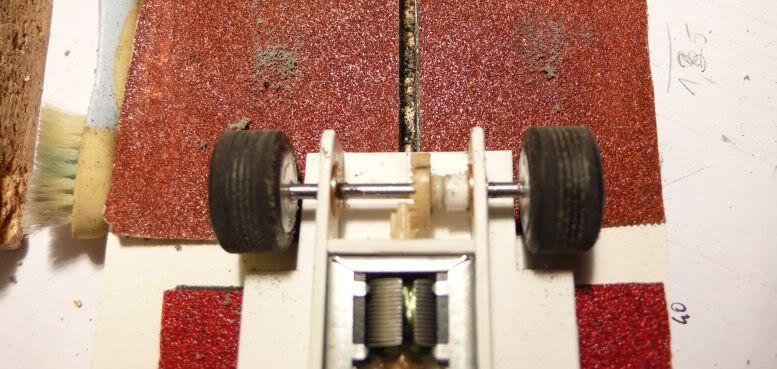
Part 7
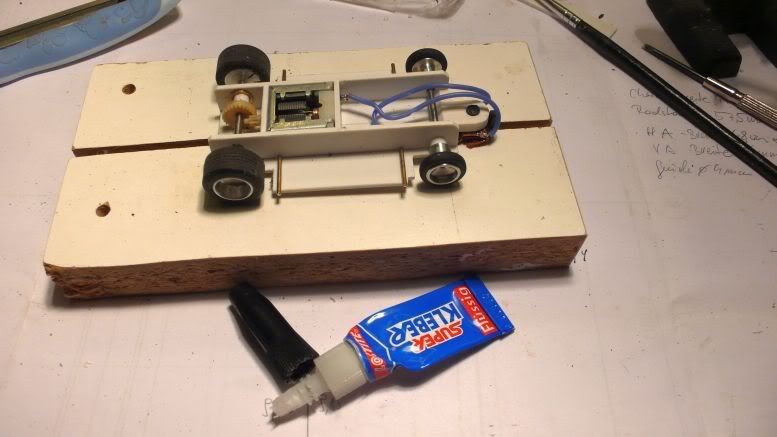
i hate it really when the CA glue is empty when i want to finish something.
Anyway, i glued short brass posts to the sides of the chassis for body mounting.
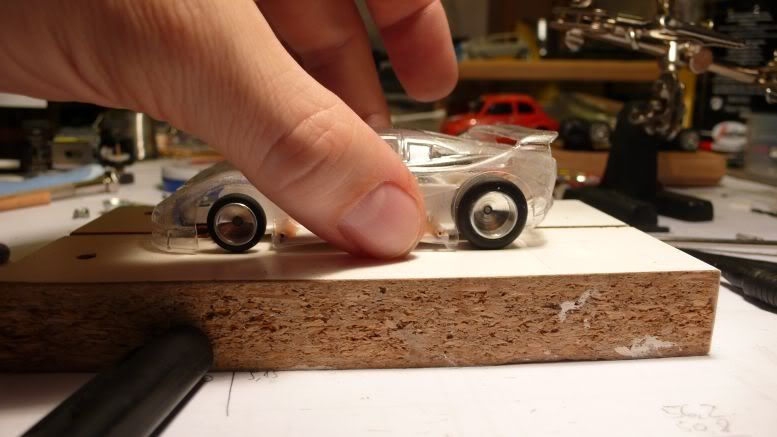
marking the positions where the holes in the body should go.
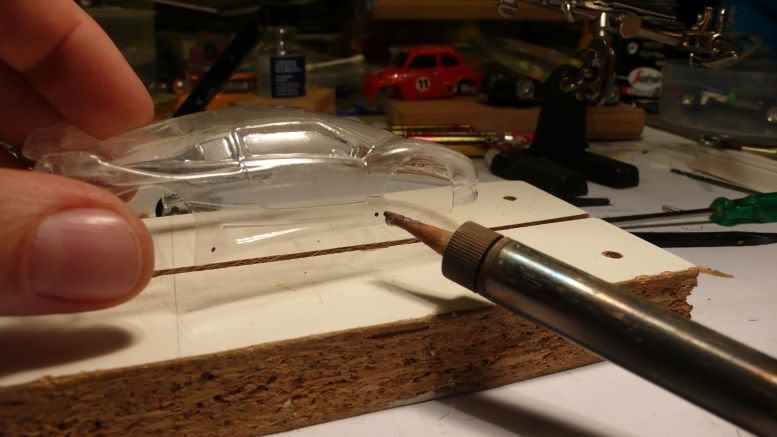
i found out that the easiest way to get the first holes into a vac-formed body is with the tip of the soldering iron. After the first holes i widen the holes with a reames of the correct size of the brass posts.
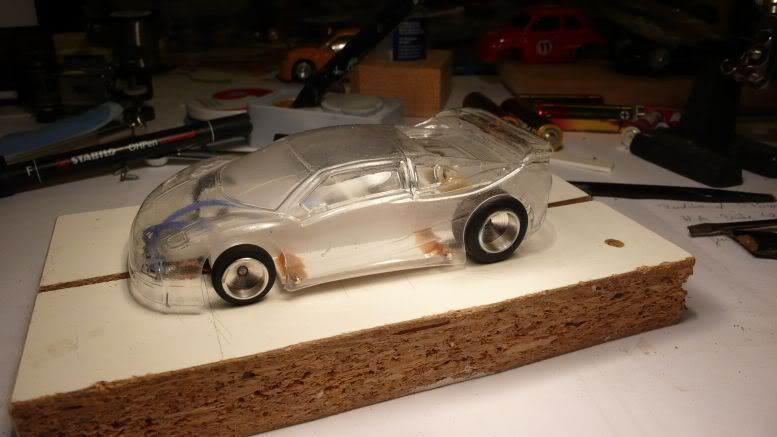
the body is mounted
END of the story